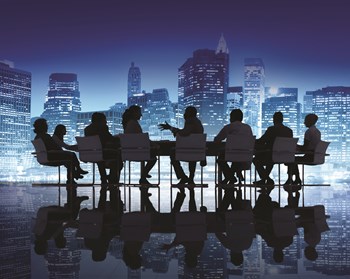
In a few months, the hot summer weather will be just a distant memory, and all that time spent trying to get cool will be behind us. Instead, co-op and condo residents will be turning up the thermostat for some soothing warmth. Now is the time to make sure the boilers that keep our buildings toasty are in good working order and ready to face the challenges of those icy winter nights.
Knowing how a boiler works and how to keep it operating at peak performance are both key to keeping co-op and condo residents happy during the long, cold months ahead. Maintaining those systems require weekly, monthly, semi-annual and annual check-ups - a rigorous schedule that may seem like a lot of work initially, but which will pay off in the long run with increased efficiency and boiler longevity, and - most importantly - contented residents.
Almost all co-op and condo buildings with more than a few units use boilers to provide for their heating needs. Boilers work on the simple principle of heating water, creating steam and then sending that steam through a series of pipes into each unit, providing an even heat for residents. Those boilers are fueled by oil or gas. "Unless the building is of a more modern design, most systems are either one- or two-pipe steam systems," says Robert T. McCarthy, president of Industrial Heat-Tech in Staten Island. With a one-pipe system, the steam goes up, becomes water, then goes back down to the boiler all through the same pipe. The two-pipe system has a vacuum. That vacuum sucks steam through the building within the second pipe. Ensuring that all those passages are clean is just one of the tasks building superintendents need to be thinking about now that fall is here.
Now is the time for managing agents, boards, and building staff to get their boiler in shape. If anything does go wrong with the system, it's best to get a repair crew in now so as not to create any inconvenience or danger for residents when it really gets cold. Pre-season maintenance can be done any time, although it's most often done between late July and September. "As we start to gear up for the winter, the boiler should be cleaned - brushed out and vacuumed - to establish the highest efficiency," says Bill Jebaily, president of Aggressive Heating and Bay Ridge Fuel Corporation in Brooklyn. "If there's dirt in the tubes, it prevents heat from conducting properly."
McCarthy agrees, adding that clean-ups should happen at least twice a year. "A lot of boards feel that cleaning once a year is sufficient," he says. "But when soot builds up, it cuts down on the effectiveness of the boiler." Not only does that mean potential heat problems for residents, it also means higher fuel bills for the building. Studies have shown that nearly seven percent of total boiler fuel costs stem from poor maintenance. "Think of the boiler like your car," McCarthy says. "You want to keep it tuned up."
It's important, too, to make sure an experienced professional is brought in to do these semi-annual inspections and cleanings. They not only have the expertise, but also the proper equipment to do the most thorough job possible. The basic cleaning process will involve wire-brushing all the fire tubes and vacuuming the entire boiler, breaching, chamber, and chimney base. A thorough cleaning can improve fuel efficiency enormously and also extend the longevity of the boiler system itself. For example, soot contains sulfur. Mixing sulfur with water can create sulfuric acid, which over time will corrode pipes and eventually the boiler itself.
After the cleaning, the mechanics of the boiler should be checked. Belts and gaskets should be tested. The boiler and tubing should be inspected for leaks. All leaks, no matter how small, should be repaired immediately. For boilers, "you should overhaul the oil burner, take it apart, clean it," McCarthy says. "Change the belts and electrical relays."
All low-water cut-offs should be checked and flushed as well. "If a boiler runs out of water, the low-water cut-offs will shut the burner down," Jebaily explains. "If a burner fires in an empty boiler, the boiler will melt."
Jebaily recommends establishing a chemical treatment program for all boilers. That means analyzing and treating boiler water to eliminate contaminants such as oxygen, which will rot away the boiler's steel.
A boiler's entire control system also should go under the microscope. If the building hasn't upgraded its system in a while, now might be a good time. "You want to make sure the control system is in good shape," McCarthy says. "If you don't have a modern one installed, you should." The top-of-the-line Heat Timer MCP Gold stands as "a very accurate" model. These systems are computerized, allowing superintendents to monitor and control the temperature levels of the boiler from a distance. "You can adjust them through your computer and really squeeze every dime out of your system," McCarthy said. That kind of efficiency can be a real boon to a building's budget, he says.
Jebaily concurs. "Once a year there should be an efficiency test," Jebaily says. "With escalating fuel prices, it's imperative to get maximum efficiency from your system. Natural gas and fuel prices have risen dramatically. A 100-unit building that may have been spending $30,000 to $40,000 [a year] to heat their building is now spending $60,000 to $80,000."
Before firing everything up, the superintendent should check the air valves on all the radiators in the building to make sure they are venting properly to get adequate heat in every apartment.
The time and expense of these semi-annual overhauls can be minimized enormously with proper daily, weekly and monthly maintenance. With proper care, boilers can last many decades. Without that care, the effective functional life of the equipment is severely reduced. McCarthy's company offers a checklist of regular maintenance for boilers. He suggests a daily visual check of the boiler room and the boiler itself, including water levels. Twice a week, low water cut-offs, pump controllers and water columns should be examined. Fuel oil levels should be checked so that the building will never accidentally run out (try explaining that one to the board in the middle of February!).
Oil filters also should be cleaned, and once a week, maintenance staff should lubricate circulator motors and bearing assemblies, clean the smoke alarm sensors, inspect compressor and oil pump belts, and check the compressor air cleaner. Twice a month, the Fireye or Honeywell scanner - the electric eye that monitors the flame - should be cleaned, all electric motors should be lubricated, and the boiler room should be swept. Once a month, the burner should be shut down and the boiler visually checked for water leaks and carbon buildup, and be sure to note the condition of the combustion chamber. The boiler pop safety valves should also be checked and the drain valves should be blown down to prevent clogging.
It is important not to forget the paperwork involved in boiler maintenance. Keeping an up-to-date boiler log is vital. Building superintendents also should make sure they have all the boiler's paperwork filed. "Make sure the Petroleum Bulk Storage certificates are up to date," Jebaily says. "They should be updated every five years." Triennial certificates - the basic boiler operating certificates - should be renewed every three years. Local Law 6291 inspections and certification should be done before the end of the year to avoid fines. "Don't wait until December to do these," Jebaily says. "It makes it very difficult to get everyone's paperwork done that way."
The list may seem long, but it's never a good idea to gamble with the mechanics of a device that can cost anywhere from $100,000 to $300,000. "Belts can break, oil pumps stop, there are sooty boilers and inappropriate water levels," McCarthy says. "Ninety percent of the problems with boilers aren't mechanical - they're human error." And that error nearly always comes from not lavishing the proper amount of care and attention on these hardworking, often under-appreciated machines.
As McCarthy says, "Good old preventative maintenance is what you want to get you through an uneventful winter." A sensible goal for any building.
For a sidebar story on a preventative maintenance schedule for your boiler, click here.
Leave a Comment