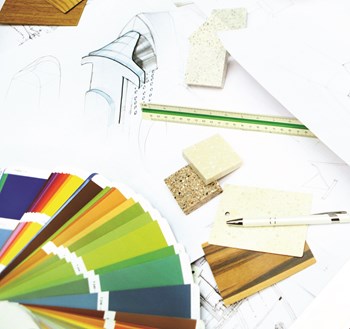
The lobbies and hallways of residential buildings are not high-end private residential projects—yet they’re not back stairwells or utilities spaces either. They literally fall somewhere in between, and no matter how new or sophisticated the building itself is, or how lavishly constructed, by the very nature of architecture and construction, nothing is exactly straight or perfectly plumb. It’s a given on any project that almost all walls, floors and ceilings will be out of alignment—it is just a matter of how much. As interior designers, we are not hired to re-build the building. We are hired to enhance its appearance, which increases value for residents, as well as attracting prospective buyers.
Cost is the determining factor when commencing a design project. Anything can be done—for a price—but it’s the building that ultimately decides the value of all options. Regardless of the final cost, once a rehab design project on any existing building is finished, issues or questions may be raised about the end result—either of the design work itself, or its execution.
While questions and differences of opinion are inevitable whenever aesthetic decisions are being made, it is important for both boards and the residents to understand what is acceptable under the interior design industry’s Industry Standards, what is not, and what is above this standard and thus more costly. Our preliminary budget estimates are based on this Industry Standard, so a fundamental grasp of the basics can help boards and management determine if the work being done in their building—and the cost they’re paying—is indeed fair and up to professional scratch.
A typical project consists of stripping the existing wall covering and doing a standard wall preparation for the new treatment. The extent of preparation depends on whether the wall will be covered or simply painted. If the contractor can determine prior to the bid that the walls need further preparation or skim-coating (a process by which a new layer of plaster is applied and polished for a smooth, even finish) the board will be advised and will make this decision. A sample area can be done in advance for review.
When we specify a grasscloth type vinyl wall covering, we expect to see a paneling effect just as you would with the real thing. This is to be expected. It is the natural material look that we are hoping to achieve.
Smooth and/or shiny wall coverings will show imperfections. A sample area is recommended for review to make sure the board and/or residents are happy with the effect. Skim-coating the walls may be necessary for the smooth look. Textured wall covering materials will hide more wall imperfections.
If deemed appropriate, new wall coverings can be hung over existing ones. It is less expensive than removing old coverings and doing wall preparation. It is imperative that the wall covering contractor examine the existing conditions to determine if installing new over existing is feasible. The walls are carefully prepared by cutting away all loose material and patching areas smooth, then coated with a primer that increases adhesion. There are situations where it is not possible to hang new wall covering over old due to the type of existing material and/or the adhesion of existing material to the substrate.
The contractor customarily smoothes out small imperfections in wall coverings—such as small lumps or pimples. It’s also common for bubbles to occur under the wall covering until the adhesive dries. The majority of bubbles will disappear, and the ones that don’t will be taken care of by the contractor. If there is a larger plaster dip or belly, however, the contractor can skim-coat the surface for an additional cost. One thing contractors may not be able to do is actually straighten walls. It is cost prohibitive and impractical. The best we can do is artfully distract the eye and live with it.
It is important to get a significant guarantee from the contractor who deems this method of installation
In cases of plaster failure, plaster may crumble and “fail” during the scraping or removal of wall coverings and surface preparation on plaster walls and ceilings. When this happens, the contractor typically has to re-plaster or re- build these areas—at an additional cost per square foot.
We recommend that if the building knows of “pops” in plaster due to moisture coming through bathroom/kitchen walls to the common hallway walls, they do all of the repair work to solve the problems prior to project commencement. Leaking roof areas and top floors should be inspected and repaired, if necessary. A survey of the building should be done by building staff.
On occasion, we observe that door saddles appear higher after installation of new carpet. These heights can vary from door to door, and should be evaluated during initial walk-through by the designer and contractors. What we see is usually the raw concrete that is the base for the saddle. When there is a visible difference, we recommend that his raw edge be painted by the painting contractor prior to the carpet installation. Another solution is to have the carpet installer lay an additional layer of tackless strip to give height to that section of the floor.
All
Proper and regular
Comments
Leave a Comment