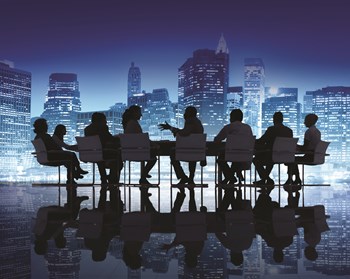
New York City law will phase out the burning of Number 6 fuel oil in the near future.
Should you wait until the last minute until making the switch to cleaner fuel oil in your own building? Does it make sense to do it now, or do it later?
The fact is that the sooner you phase out Number 6 fuel oil, the more money you will save. There are several ways of phasing out Number 6 fuel oil. An easy way is to tell your fuel oil company that you want to burn the Number 6 fuel oil that you have in the tank until it is almost empty, pump out the remaining Number 6 fuel oil, clean the tank, and fill it up with Number 2 fuel oil. You would then disconnect the heater for the Number 6 fuel oil, set up the fuel pump to run only when the burner is running, and change the burner nozzle and replace the fuel filter. You could also do any other work that your service technician recommends at the time.
While Number 6 fuel oil has more BTU per gallon than Number 2 fuel oil, l45,000 BTU per gallon compare with l38,700 BTU per gallon for Number 2 fuel oil, the reduction in the
parasitic losses from handling the Number 6 fuel oil by preheating it and running the fuel pump continuously would make up some of the difference in net operating costs.
Also, Number 2 fuel oil burns cleaner than Number 6 fuel oil, so at the time of conversion, you would need to clean the boiler tubes to remove the soot on the fireside of the fire tubes.
One Building's Story
Two years ago, I prepared an engineering study for a ll6-unit apartment building on the East Side of Manhattan near the United Nations. The building was burning Number 6 fuel oil. For the 2008 calendar year, the boilers burned approximately 47,942 gallons of Number 6 fuel oil; thus the fuel oil usage was 413 gallons per unit per year.
The boilers were original to the building which was built about l965. There were two Federal firetube firebox-type boilers each rated at l34 boiler horsepower. Each boiler was fired by a 50-gallon per hour Johnson rotary burner.
As part of my engineering study, I performed a combustion efficiency test on the boiler in use at the time. The stack temperature was 450 degrees F, and there was 4 percent carbon dioxide in the flue gas. The steady state efficiency of the boilers was 66 percent.
The super told me that prior to the installation of low-E windows in the building, maximum fuel oil consumption on a cold winter day was approximately 450 gallons.
A review of recent consumption records noted a maximum daily consumption of about 300 gallons per day, a reduction of about one third.
At a firing rate of 50 gallons per day, each boiler in the building can burn 1,200 gallons of Number 6 fuel oil per day. Of the 300 gallons of fuel oil burned each day in the coldest weather, l00 gallons is lost in stack losses. Thus, only 200 gallons equivalent of BTU in the oil is necessary to heat the building.
It is illegal in New York City to install a new burner that can fire Number 6 fuel oil at less than 20 gallons per hour. Thus, the only alternatives that made sense in this case were natural gas or Number 2 fuel oil. According to Con Ed a large uptick in natural gas usage would have necessitated the digging up of the street back to First Avenue to install new gas mains, as the present mains could not support additional service.
In light of all this, my recommendation to the owner was to install two new high efficiency boilers rated at l0 gallons of Number 2 fuel oil per hour. If we divided 200 gallons by 24 hours per day, the building only needs the equivalent of 8.3 gallons equivalent per hour to heat the building. Assuming a boiler efficiency of 83 percent, one could heat the building with a new boiler with a firing rate of l0 gallons per hour. I also recommended that all the steam traps be changed at the time of installation of the new boilers and that changes be made to the condensate return system so that a gravity return system take the place of a condensate receiver tank.
Energy and Cost Savings
The cost of conversion for the East Side building was projected at $100,000. This cost included removal of the old boilers, installation of new boilers,and commissioning the new boilers to run on Number 2 fuel oil.
Energy savings from combustion efficiency savings were estimated at ll,744 gallons of Number 2 fuel oil per year. Off-cycle savings, when the burners were not firing, were estimated at 10,l94 gallons of Number 2 fuel oil per year. Total energy savings were estimated at 21,938 gallons of Number 2 fuel oil per year. Usage of Number 2 fuel oil was projected to be 28,688 gallons per year, or just 247 gallons of fuel oil per unit per year.
Even with a cost differential of $.3575 per gallon between Number 2 and Number 6 oil, the fuel oil cost savings were projected at $9,827 per year. An additional $3,000 per year savings per year was projected from a reduction of electrical usage.
Total cost savings was projected at $12,827 per year at the time of the study. The simple payback period was 7.8 years. With today's fuel oil costs, the payback period would be between 4 and 5 years. So even though the initial cost and work might have seemed daunting, over the expected life of the boiler, it certainly pays to replace sooner rather than later.
Daniel Karpen is a professional engineer based in Huntington, New York.
4 Comments
Leave a Comment