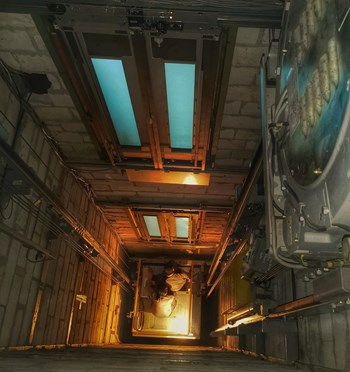
The elevator is one of those inventions—along with running hot and cold water and indoor plumbing—that have been around for so long we take it for granted. But elevators obviously weren’t always a part of the architectural landscape. Without them we’d still be living in a world of six-story buildings (maybe seven for the strong-legged), and we’d be climbing stairs all day long. That might have a beneficial effect on our general fitness levels, but it would also be extremely inconvenient—not to mention making upper floors inaccessible to anyone with health or mobility limitations.
A Short History
There are competing claims to the origin of elevator technology. One version of the story credits Werner von Siemens, who built the first elevator in Germany in or around 1880. The technology spread to Austria-Hungary quickly, and by 1889 inventor Anton Freissler added doors and improved the technology sufficiently to build a thriving elevator business in Central Europe.
The Otis Elevator company claims it can trace its origins to 1853, when Elisha Graves Otis presented the first elevator at the Crystal Palace Convention in New York City, on the site of what is now Manhattan’s Bryant Park. His invention led to the first installation of an elevator in a New York City property in 1856.
We’ll let the heirs of each claimant duke it out. What matters most today, says Darin Cook, a partner at the New Haven, Connecticut, office of Pelli Clarke & Partners, an international architectural firm with offices in the U.S., China, and elsewhere, is that the invention of the elevator unlocked the capacity to build much, much taller than just six or seven stories.
“Before the elevator,” says Cook, “buildings typically did not exceed eight stories. For taller buildings you needed an elevator. It was that simple. Vertical transport as afforded by elevators provided for higher density and populations within buildings.
“The technology has evolved over time,” he continues. “The first elevators were more like an industrial conveyor belt.” For instance, German elevators in the 1920s often moved continuously—if slowly—and didn’t have doors; you literally stepped on and off as the cab kept moving. “Everything from brakes, to cables, to pulley systems has been augmented to make [elevators] safer, and to make people feel safe riding them. That’s an ongoing thing. Today’s state-of-the-art is speed.”
Joe Caracappa, president of Sierra Consulting, an elevator consultancy based in Manhasset, New York, has been active in the elevator industry for more than 32 years. He maintains that the introduction of the elevator as a standard component of building design changed all aspects of construction technology. “It allowed for buildings to be built high instead of wide,” he says. “And in tandem with the innovation we know today as the curtain wall and its introduction, it changed the way foundations were built as well, making them far less massive.”
How Elevator Systems Work
While they may appear complicated to the untrained eye, including this reporter’s, elevators are more mechanically straightforward than they might seem at first glance.
“There are basically two types of systems,” says Caracappa, “cabled and hydraulic. Cabled means the system is powered by an electric motor. Machinery lifts the cab, which is counterbalanced by a weight up and down the shaftway. That’s the most traditional system. A hydraulic system is oil driven, and is usually found in low-rise buildings, meaning those under five stories. It requires that oil be pushed into a piping system to raise the elevator—so past a certain height, that becomes difficult to do. You find hydraulic lifts in doctor’s offices or stores which are two or three stories high. In New York City and other locations with high-rise buildings, cable systems predominate.
“Sometimes within a taller building, a separate, secondary system is required,” Caracappa continues, “for, say, a doctor’s office on a low floor in a mixed-use building. Hydraulic systems are, overall, a low-rise application. The cable system is a better technology. You don’t worry about oil spillage, and cable is also more electrically efficient and poses less risk overall.”
Of course, while the fundamentals of elevator engineering may have stayed more or less the same over the decades, certain features and functions have been added or upgraded as technology has advanced. “In high-end residential and office buildings today,” says Cook, “there is something called destination dispatch which essentially uses technology to detect how many people are coming into the building, and will assign which cab the passenger should get onto based on the flow of people coming and going. You don’t press an ‘up’ button in these systems. Rather, you enter your destination within the building into a pad on the wall and a computer selects the best cab for you and directs you to it. This system moves people in and up and down as quickly as possible. That’s its purpose.”
In another innovation, Cook explains that traditionally, elevator controls were in machinery rooms located either on the roof or in the basement of buildings. “Now the controls are often on top of the cab and direct the elevator from there. This is called a machine-room-less elevator.” Relocating the controls is not only more convenient for maintenance and repairs, it makes them less vulnerable to the elements (in the case of rooftop positioning), and flooding (as sometimes happens in basement locations).
Care & Maintenance
The regular care and maintenance of your elevator machinery and cab is provided by an elevator maintenance company under a contract. Cook points out that the contract is a part of choosing a cab and machinery. “We work with developers of skyscrapers, high-end residential luxury buildings, and offices,” he says, “and almost all projects require at least three to four potential manufactures for best price purposes. There are a good number of vendors out there, and we have to plan for all variables. Depending on the client, we may only want to use a certain manufacturer. We also know the maintenance contract comes with the elevator cab provider. They provide the service. When we specify a certain manufacturer, the developer must be aware of the contract being included. That may provide pricing differences between cab and contract with different users.”
“Maintenance is extremely important now,” adds Caracappa, “as users are trying to extend the life of their elevators. It’s important that you get a copy of the maintenance agreement, and that it fully covers all the components for the type and style of elevator in your building. What’s different now is that capital work has been affected by both high interest rates and the many new rules and regulations pertaining to a building’s carbon footprint. The work to be done can be unusually demanding in terms of cost, to say the least. The average cost of elevator replacement is now very high—so buildings are trying to figure out how to continue operating with what they have, instead of doing a complete replacement. They’re reviewing their current systems to see where they stand, and to extend their useful life.”
Caracappa describes the typical elevator maintenance routine as follows: “Every property has a contract with a service provider, which is required here in New York City. Maintenance is performed monthly. Different parts of the systems are maintained through the year. The doors, for instance, are done at a certain time. Lubrication of cables at another time. The cleaning and lubrication at other times of year. A log book should be placed in the mechanical room that each technician fills out and details what tasks were done and at what frequency.”
Challenges
In addition to the ever-increasing cost of maintenance and replacement, climate change has forced buildings to face other challenges today that weren’t even considered a few years ago. “All buildings have to have emergency generators for power outages,” says Cook. “All cabs are designed to go to a home return floor in case of, say, a brownout. They will automatically return to ground level, and then they stop operating. In power surge situations, there are systems built in to keep riders from getting trapped. With storm surges becoming more common, we’re starting to move the elevator control systems and generators off the ground floor to the roof, or the third or fourth floor in new buildings to prevent flooding.”
While the elevator’s ubiquitousness may be a fact of our daily lives, replacing even a relatively simple system can pose a serious financial challenge to all but the wealthiest buildings—so that makes regular, thorough, and, most importantly, expert care and maintenance critical.
A J Sidransky is a staff writer/reporter for CooperatorNews, and a published novelist. He may be reached at alan@yrinc.com.
Leave a Comment