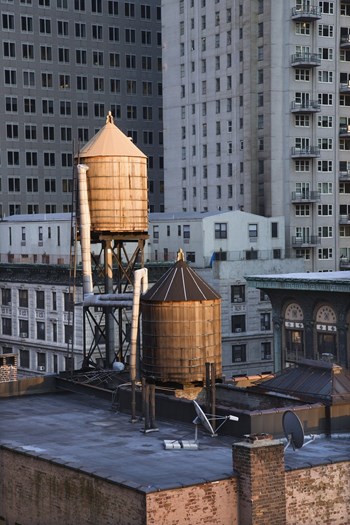
While they may seem like archaic pieces of urban art—if they’re noticed at all—rooftop water tanks serve a vital function to countless high-rise buildings in New York City. Whether made of wood or steel, the care and maintenance of these all-important fixtures falls to a handful of niche companies catering to this often over-looked industry.
Tanks for the Memories
“The original purpose of roof tanks was to supply drinking and bathing water to people living above the sixth floor,” says David Hochhauser, who along with his brother and sister owns Isseks Brothers, a tank servicing company based in Lower Manhattan. “Prior to the invention of the elevator, buildings were not built over seven stories.”
In the late 1880s, when the elevator was introduced, New York’s iconic skyline began to take shape. While building vertically was a progressive approach to city planning, the height water could reach without assistance was limited, and thus posed a challenge to the growing metropolis. “My great grandfather adapted his skills as a cooper in Eastern Europe, and developed the concept of the roof tank,” explains Hochhauser. “This allowed water to be pumped up to whatever height the building was, and then gravity fed to those below. His firm was the first to install a roof tank in the late 1880s.”
Hochhauser’s is one of only three companies in New York that still works in this industry. These family-driven businesses, realized across many generations, hold to the adage “if it ain’t broke, don’t fix it.” To this end, water tank construction has not varied that much over the decades, says Steven Silver, vice president of American Pipe & Tank Lining Co. in Long Island City. “The tanks have not changed; however, with the invention of power tools, the construction became quicker,” he notes.
Andy Rosenwach, whose great-grandfather Harris started the third firm specializing in roof tanks, the Rosenwach Tank Co., (part of the Rosenwach Group family of companies), provides more history on the industry. “In prewar buildings, the piping is arranged where the lower floors are fed by street pressure and the upper floors are fed by the gravity tank. In postwar buildings, the entire building is fed by the gravity tank. The tank serves two purposes: providing water for washing and drinking, and providing water for fire suppression to standpipe outlets in stairwells and or sprinkler heads.”
Rosenwach adds that as pumping stations became better built, the majority of buildings 12 stories or less do not require a gravity tank. “The gravity tanks are used in today’s designs primarily in taller buildings for domestic use, fire suppression and storm water retention and detention,” he says.
Wood, Steel & Technology
It is not by coincidence that rooftop tanks are made from the aforementioned materials. “New York City building codes only permit wood or steel for the construction of water storage tanks,” says Silver. “Therefore, Manhattan buildings have both wood and steel tanks.”
Over the years, the construction of water tanks has become streamlined and more efficient, which has allowed cost savings. In the case where combined gravity tanks equal or are greater than 15,000 gallons, two separate compartments are required. Rosenwach Group, for example, has engineered the two-compartment wood tanks. And while technologies have developed that include digital readings for water level and temperature that can include local and central supervisory monitoring and enhanced security monitoring, the initial roof-tank concept hasn’t changed.
“Most tanks positioned outside the building on the roof are made of wood,” says Rosenwach. “Wood is a natural insulator. In the summer, the water remains cool and in the winter, with circulating systems, does not freeze.”
Hochhauser explains that the majority of the city’s approximate 10,000 rooftop water tanks are made from either cedar or redwood. The advantage to wood over steel, he says, is that wood is much easier to maintain, delivers cleaner water and can be replaced in just one day. “Typical life expectancies of wood tanks are between 20 and 25 years, depending on the quality of lumber used and the location and orientation of the tank,” he notes.
Rosenwach adds that steel tanks are use primarily inside buildings to maximize capacity. “A rectangular steel tank holds more water than a round wood tank, both having the same height,” he says, noting that replacement tanks of either material cost around $50,000.
The construction of a new tank or the rebuilding of an existing tank is a considerable undertaking, but when done properly reduces downtime for building owners. An existing wood tank can be dismantled within several hours. The bottom of the new tank is assembled very much like a dining room set, says Rosenwach. “The staging is built. Pipe connections are replaced as required. Within another three hours the staves—or walls—of the tank are assembled. The hoops are then installed and tightened” just like a giant wine barrel. In most cases a project started at daybreak can be completed by 5 p.m. with the water tank ready for filling. Finally, he says, the cover is installed.
In many cases, all three tank companies take a “green” approach to dismantling old roof tanks and find ways to repurpose the materials. “We have donated the old tank lumber...to wharfs and architects for specialty projects,” says Rosenwach.
Operation & Maintenance
With regard to operation, Rosenwach explains that typically a pump station is located in the basement, which takes the water coming from the city pipes and pushes the water up into a roof tank. “The roof tank is controlled by electronic sensors that operate the pump station when the tank is low to fill the tank, and monitor level and temperature.”
Generally, wooden tanks require less maintenance than steel models; however, the city requires that they be cleaned on a yearly basis. During this time, Hochhauser says that the tank covers, pump control switches, steel supports and pipe insulation are checked to ensure all components are in good working order. “Most tank companies do not charge for inspections, so boards or managers should call a licensed company if they suspect something is amiss,” he says. He adds that the typical costs for city compliance for water tanks averages about $1,000 per year, not counting mandatory water testing.
Philip Kraus, CEO and owner of Manhattan-based Fred Smith Plumbing & Heating, notes that monitoring of rooftop water tanks falls under the purview of two agencies. “The regulation of the cleaning and inspection of water tanks is provided by two separate New York City agencies: the Department of Buildings and the Department of Health. Building owners should comply with the regulations of BOTH agencies, not just one of them,” Kraus says. “The DOB (through the New York City Plumbing Code) and the Department of Health (through the New York City Health Code) provide regulatory requirements for the maintenance and sanitation of the tanks.”
He notes that the plumbing code orders all tanks to be “drained and cleaned at least annually,” while the health code requires annual tank inspections. The inspection, Kraus says, under the health code purview is a visual inspection of the sanitary conditions around the tank, for example, if there were sediments, biological growth, and/or floatable debris like insects, rodents or birds. A water sample is also done to “verify the bacteriological quality of the water” in compliance with the New York State sanitary code.
While most maintenance on the tank structure and mechanisms themselves should be handled by professionals, there are visible tell-tale signs of problems that building staff, such as supers or engineers can keep an eye out for. Silver explains that these include “heavy leakage, as well as heavy growths of moss and algae on the outside of the tank.”
When asked what are some of the more common maintenance and upkeep problems impacting roof tanks, and how they can be avoided, he responded: “Unfortunately, the most common problems are related to the roof tank repairs, which are typically unavoidable due to Mother Nature — such as high winds, storms and hurricanes.”
The maintenance of wood tanks requires a company to be licensed by the city to both clean and maintain them. In recent years, there have been more companies technically unqualified to handle maintenance problems, notes Hochhauser.
“Recently, we have seen a proliferation of traditional plumbing companies trying to capitalize on the city’s increased vigilance in enforcing their health codes with respect to the cleaning of the domestic tanks yearly,” Hochhauser continues. “What most condo/co-op directors don’t realize is that these plumbers do not have the requisite confined space training. If a worker gets hurt, or gets stuck in the tank, the building will ultimately bear the responsibility if the company they engaged did not have the proper training and credentials.”
All buildings must adhere to S12 and S13 city codes for sprinkler and for standpipe reserves, respectively. These are monitored by the New York City Fire Department (FDNY). Rosenwach notes that one recent code also requires that “if a tank has a float valve and or an automatic float switch that this tank must be equipped with a high alarm.” And, he adds, that “as of 2008, the FDNY also requires that the fire reserve tanks in cold weather indoors and outdoors have a temperature-monitoring device.”
The Inspection Process
When asked what steps co-op and condominium boards should take to ensure they are in full compliance with city regulations, while ensuring that respective roof tanks are operating efficiently, Silver says a three-tier approach is recommended. “Clean and disinfect tank interior. Perform internal and external inspections, and take water samples,” he says.
Rosenwach adds that the certificate holder for the building can inspect the exterior of the tank,” but reiterated that “the annual cleaning of the tank must be handled by a licensed professional plumber and/or sprinkler contractor,” who have the proper certification.
Most annual inspections are done by one of the city’s water tank companies or by licensed master plumbers or inspectors certified by the Department of Health and Mental Hygiene (DOHMH). An inspector checks for damage to wood or structural steel, water leaks and for things such as foreign objects, pigeons or other vermin that might have gotten into the tank. Cleaning an average-size tank takes about four hours and costs around $1,000.
Kraus notes that unlike the plumbing code, the health code doesn’t require an actual cleaning, unless it is deemed necessary as a corrective action to an unsatisfactory visual inspection, and/or or failed water test. In fact, if a building’s tank passes the visual inspections and the water test, the health code doesn’t technically require an annual cleaning.
Kraus also says that only the Health Department, through the health code, requires a written report documenting the results of any inspection be maintained by the owner of the building for at least five years and made available to the DOHMH upon request within five business days. The health code also requires building owners to post a notice for residents that inspection results are available upon request.
There was a January 2014 New York Times article that examined the conditions inside some of the city’s water tanks where investigations found the presence of bacteria. According to the Times article, “Samplings taken by The New York Times from water towers at 12 buildings in Manhattan, Queens and Brooklyn found E. coli in five tanks, and coliform in those tanks and three more. Coliform by itself is not harmful, but does indicate that conditions are ripe for the growth of potentially dangerous microorganisms. The positive results all came from the bottoms of the tanks, below the pipe that feeds the buildings’ taps, though public health experts say the contamination is still a concern because the water circulates throughout the inside of the tanks.” According to the Times, when contacted, spokespersons for the Health Department said the “methodology” and the conclusions drawn by the newspaper were “flawed.”
While alarming, Kraus also thinks there is not a major problem. “The horrible conditions of rooftop water tanks outlined in the New York Times article are extreme based on our experience,” he says. Most of the buildings that his company services, he continues, have roof tanks that are well maintained and regularly cleaned. “And, so long as the Health Department continues its spot checking of the buildings for the annual inspection results and the boards of the buildings ask to look at the inspection report, this should be enforcement enough.”
Board members should also ensure that management companies and employees are vigilant in watching the tank to ensure it’s not overflowing as a loss of water equates to a loss of money, says Hochhauser. “And,” he adds, “make sure that the hi/lo alarms in the basement are working properly.”
W.B. King is a freelance writer and a frequent contributor to The Cooperator.
2 Comments
Leave a Comment