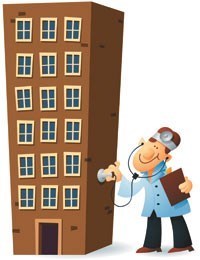
While residents may breathe a sigh of relief when winter and its piles of snow, slushy puddles and blasts of arctic air finally exits the scene, co-op and condo buildings can’t always shake off the ravages of the season so easily.
From leaking roof membranes to dirt-infused carpets, winter’s effects need to be addressed as soon as weather permits. The waning days of winter present managers and supers with the opportunity to inspect the property and plan needed repairs.
Unfortunately, building boards and managers who haven’t lined up a host of professionals to attack those problems well in advance may find themselves scrambling to close the door on winter and prepare for the coming spring. By the time city trees begin to show hints of green, contractors already have their work lined up and their schedules filled.
A Top-to-Bottom Review
Wayne Bellet, president of Manhattan-based Bellet Construction, says exterior inspections should be on a building’s schedule year-round. Doing a basic examination of the property three times a year, he says, can catch small problems before they become large ones.
Starting at the top, Bellet says that a walk on the roof—with digital camera in hand—can unearth a variety of potential problems. “When you walk the roof after the season changes, look at it with new eyes, evaluate it, and then do it again four months later,” he suggests. Things to look for include clogged drains, open bulkhead doors, loose railings, and frozen turbine vents. Check for exhaust fan motors that have seized up. Look for roof membrane that has bubbled, 'alligatored' or cracked, and for openings around the base of vents.
The inspection, he says, is something the building super or handyman can handle. “I tell people to take a digital camera, and take pictures of everything,” Bellet says. Photos will not only document problems, but also prove that the inspection was actually done, and that various components were examined. “Make a checklist,” he suggests, noting that his company gives its customers a worksheet for free.
“It’s like going to the dentist,” Bellet says. “Most people don’t want to do it, they put it off, and by the time they find a problem, it’s like needing a root canal.” Damage to the roof can be insidious. If caught early, repairs can be reasonable, but once the damage expands, moisture gets in and the repair becomes a major project. “You’ve got to demolish it. And usually, you’ll have to do asbestos removal,” he laments.
Moving down the building envelope, Bellet says the super or handyman should open a window and study the sealant (caulking) around the frame. Most sealants, he says, have a life span of about five years. “Look at the window sill, and especially around the window air-conditioning unit.” If the caulking looks dry, or cracked, “face it, it’s not going to get any better; it’s not going to heal by itself.”
And if the sealant around one window is bad, chances are that it’s also bad around all the other windows since they would have been installed at the same time. When danger signs begin to appear, it’s time to start putting some money aside for the inevitable repairs.
Walk across the street—still with that digital camera in hand—and take a look at the building’s exterior, from the cornice at the top all the way down to the sidewalk.
Also look for snow and ice buildup on entrance canopies, which could pose a danger to passersby with melting and refreezing issues. Also water drains onto sidewalks below creating slippery surfaces for pedestrians.
And speaking of sidewalks, Bellet decries the all-too-common heavy hand used in spreading salt in wintry weather. The salt may help prevent expensive slip-and-fall accidents, but it also destroys the concrete. Sidewalk squares also tend to lift with the freezing and thawing cycles, leading to tripping hazards—and fines from city inspectors. They need to be fixed.
A building may not be able to avoid the ravages of winter but regular reviews and maintenance can keep small problems from becoming big ones. “By monitoring the building after winter, and comparing the pictures you take after every season, you can see how you’re doing,” he says.
Looking Up
Few parts of a residential building are as important as the roof—it helps maintain the temperature in the building no matter what the thermometer reading says, protects its contents from the ravages of leaks and water damage, and literally keeps the rain off residents’ heads. A neglected roof is a liability—it hemorrhages money in the form of constant stopgap repair work, damage to property, and possibly even legal action brought by angry shareholders. Most roofs last from around 10 to upwards of 25 or 30 years, depending on various factors.
Another key rooftop element is the ubiquitous water tank that dots the city’s skyline. Generally in New York City, a roof tank serves as a storage system for domestic water and as standpipe water for firefighting.
“Cedar tanks last 30-35 years generally, prior to requiring replacement,” says Andy Rosenwach, owner of The Rosenwach Group, a roof tank and building maintenance company located in Long Island City. “Wood becomes spongy with algae growth. Tanks start to leak” and eventually need replacing, he says, and adds that several factors can shorten the life span, including exhaust from cooling towers and boilers, as well as damage from birds, which may cause unnecessary deterioration and affect the water quality.
On the other hand, new technologies and improved building materials may help to extend a tank’s longevity, Rosenwach says. “When it comes to a water tank it is advisable to allow the tank to go the distance. With today’s new controls and roofing materials a tank should require minimum repairs during the course of its life span. The cedar roof tank should be replaced at a minimum of 30 years after installation. Budgeting should be done from this time frame.”
Record keeping is an essential part of the maintenance process for roof tanks, too, says Rosenwach. Records should be kept on the year the tank is installed; the fire-rated reserve capacity; the number of annual cleanings and bacteria testing; and how often the pipe is replaced during the course of the tank’s life span.
Getting the Best Price
The off-season inspections and preparation aren’t just a way for managers to keep busy when winter winds are howling. They’re also a way of keeping a lid on costs, says Rosemary Paparo, director of management for the Manhattan firm of Buchbinder & Warren. “You get the best prices in the winter, because they want to be able to start, come the good days in the spring,” Paparo says.
Just as building managers are preparing for the coming work season, contractors are lining up jobs, filling their calendars. “They all—no matter how large they are—they have a limited number of jobs they can take,” Paparo says. “If you get pressed for time at the end (of winter), your price as a client is going to go up” as the exterior work season approaches.
“So what we like to do is spend the winter strategizing how it’s going to be done, and then negotiating with the contractors, so that we have everything in line. The architects are in place, the contracts are in place, they’ve pulled the permits and they’re ready to go.”
“We like to have our contracts wrapped up in February, especially if it’s a Local Law 11 project,” says Paparo. Reports produced under the city’s façade-inspection law “come with a list of things you have to do,” and building managers want to be ready to roll on those projects as soon as the weather allows.
Local Law 11 functions on a five-year cycle and requires all buildings over six stories tall to have their inspections simultaneously—which is why the city of New York seems to sprout sidewalk sheds like a plywood contagion every five years. The inspection must be done by a licensed engineer or architect retained by the owner of the property.
“There’s always a spate of exterior work when you have one of these Local Law 11 years,” she notes. To prepare for the spring work, “everybody will be getting everything together, negotiating contracts. They have to get the specs ready, so they‘ll be ready to go in the spring.”
All eyes are on the weather, and the thermometer, as winter retreats and spring starts to creep in. While workers are anxious to get started on the façade work, ranging from sill replacement to parapet repairs, safety considerations and the temperature-sensitive nature of some repair materials will determine when those jobs can get under way.
The same preparation schedule should in place for roof work, air conditioning checks, water tank replacements and heating plant projects, Paparo notes. While emergencies may arise, most of those projects can be planned well in advance. “You do the same thing: Do the contracts in the winter, because with a heating plant you want to start putting it in at the end of May, beginning of June.”
In fact, Paparo says, heating system contractors have been in especially short supply, with the heightened interest in converting from oil to natural gas. Projections are that gas “is going to be appreciably less expensive than oil, so it’s really a no-brainer. Con Ed has a backlog,” Paparo says. “Last year, we saw for the first time, heating contractors that have been around for a long time, reputable companies, couldn’t even take on new jobs because they were getting so many requests for proposals.”
Maintain Now—or Pay Later
While major projects are on the schedule for many buildings, regular maintenance should be high on every manager’s and super’s list, says John Sideris of New York City-based Sideris Plumbing and Heating Corp. “The big thing is maintenance on pumps that have been running all winter,” he says. “You need to lubricate all the pumps at the end of the heating season, just like you did at the beginning of the heating season.”
But, he says, “most condo and co-op supers don’t do it.” Larger buildings with full-time supers are more likely to keep up with that type of maintenance, while it often slips by at smaller buildings. “You end up,” he says, “with thousands of dollars of replacement costs.”
Along with the end-of-winter maintenance, Sideris says it’s a good idea for co-op and condo boards and managers to take a post-heating season look at their energy costs. The time spent on a review of the winter’s expenses can not only pinpoint potential problems, but also spur ideas for future savings. “If you do that inspection in the spring, he says, “you’ll save headaches next winter.
“When you shut the boiler off in the spring, if you bring in a professional, you may find problems you can nip in the bud and make the repair smaller, than if you wait for the winter, when you start it up again,” says Sideris, who has been in the heating business for 35 years. Once the heating system begins, buildings are under pressure to make repairs. With an off-season review, there’s time to explore alternatives.
By reviewing fuel bills from the heating system, he says, it’s possible that a professional can recommend ways for a building to save money. “Most systems are antiquated,” he says. But rather than consider updating those old systems, “people leave it alone; they don’t rock the boat. But the fuel they could save if they invested a little is tremendous. There’s technology today to make these systems far more efficient.”
Too often, he says, building managers or supers think about their boilers at the end of summer, just before the heating season begins. “Fall is too late, especially with co-op boards. Decisions can’t be made fast enough,” Sideris says. “But if it’s done in the spring, the payoff on that investment can be tremendous.”
Also on Sideris’ list for end-of-season maintenance: sprinkler systems. “The main valve should be lubricated, but nobody does it; they wait for them to leak.” Skipping that simple maintenance job, he cautions, can be costly—or worse. “The valve may not work when you need it, God forbid,” he warns. At the least, “you save an expensive repair. An ounce of prevention is worth of pound of cure.”
Pat Gale is associate editor of New England Condominium, a Yale Robbins’ publication.
Leave a Comment