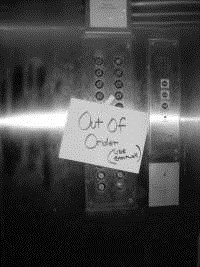
Every property manager has a horror story or two—or three, or four, or forty-seven—about the sub-zero winter night when the boiler in a 400-unit high-rise went kaput, or what happened when the sprinkler system decided to turn on for no discernible reason and drenched several newly-remodeled hallways, or the spring rainstorms that helpfully revealed the dire condition of the building's World War II-era roof by flooding the penthouse owner's collection of Picassos. Even the best-maintained buildings sometimes experience what might be called maintenance meltdowns, and when disaster strikes, it's up to the management, board and building staff to get things under control and back on track as quickly as possible.
Let's take a look at some major maintenance meltdowns, and how they were handled.
MELTDOWN #1: Don't Smoke in Bed
The Scenario: A few years ago, a 42-story co-op apartment building caught fire in the early morning hours after a resident fell asleep while smoking. The blaze claimed the life of the smoker and her husband. Thankfully, no one else was injured, but the damage was severe. Smoke and water wreaked havoc on the building, which had just completed a significant renovation. The insurance claim was in the seven figures, and it took nine months before the repairs were completed.
Michael Berenson, president of AKAM Associates, Inc. in Manhattan, was the building's property manager—and he was prepared for the unexpected.
His crisis management team, comprising various experts who were assigned to deal with different aspects of the problem, responded with speed to the crisis.
"We were coordinating with the fire department, the building department, insurance carriers, and working with shareholders," he says.
The fire happened at 5 a.m. AKAM's team was on site within a half hour. An entire clean-up crew was there within two hours.
"When residents need you the most, that's when you have to be there," Berenson says. "The most important thing is to minimize the stress for the shareholders."
Communication at all stages of the event is imperative as well. "We had a meeting the next night after the fire with the insurance company there and the heads of the clean-up and construction crews," Berenson says. The meeting gave residents the opportunity to ask questions and also helped them understand that work was already underway to try and restore their lives to normal as quickly as possible. "You have to make sure that shareholders are aware at all times of what's happening and what's being done."
The Lesson: Being prepared before the fire helped minimize damage, too. "The building has always done education on what to do in case of a fire," Berenson says. Information packets and updates, which were provided on a regular basis before the fire, were handed out again as refreshers. "When you live in a high-rise building, you always have to be aware of what to do in a fire," he says.
Berenson urges all buildings to have an emergency plan. "Not just a fire safety plan, but an overall emergency plan that is prepared for each property," he says. Trying to think ahead and plan for as many contingencies as possible will pay off in the long run, both in terms of resident safety and in terms of preserving and protecting the property.
MELTDOWN #2: The Walls Come Tumbling Down
The Scenario: It began in a bathroom. Not just the toilet or the tub—the entire bathroom. One morning, out of the blue and apropos of nothing, the entire bathroom in the super's first-floor apartment collapsed onto the street. Fortunately, no one was using the bathroom at the time, and no one was hurt. But that didn't change the fact that the bathroom had completely collapsed.
The reason for the collapse was not water damage, as you might expect. No leaky faucet had done its dread work on the beams, nor was there an infestation of termites. The building is on an incline, with an exposed rear and open foundation. To compensate for the hilly topography, struts were used, for added support. Those support struts had just given out, for no discernible reason. The first casualty was the super's bathroom. Would the second be the entire building? Would the co-op be—gulp—condemned?
The property manager, Gregory Cohen, the president of Impact Real Estate Management in Flushing, quickly called in the cavalry.
"The fire department came down, brought the collapse team," he recalls. "We called our architect and our engineer, and had them at the scene. We brought in a structural engineer."
The verdict? "It was the support struts, not the building support," Cohen says. "It was just the first floor, not the entire building."
Repairs began at once, and the super's bathroom was quickly back in working order.
The Lesson: While there was not much anyone could have done about this particular case—"There was no evidence of rotting before it occurred," Cohen says—structural problems like this are not uncommon.
Periodic inspections, especially in older buildings, can help prevent disasters before they occur. But structural problems do not only befall older buildings. Shoddy work during renovations in new buildings—in brand-new buildings, sometimes—can also be an issue. This can occur when boards try to cut corners on contracting projects.
"Boards will spend $100k to do work, but they won't spend $10 or $15k to hire an engineer to make sure the work is done properly," Cohen says.
The results can be devastating. One building spent a quarter of a million dollars on renovations, only to find that more than half of the work needs to be redone.
"The best way to avoid issues—hire an engineer to do a set of specs on what needs to be done," Cohen says. "Then, bid it out. Two from the management company, two from the board, two from the engineer. The sealed bids should be sent to the board. The board should open them with the managing agent, altogether, at the same time."
This may not prevent unforeseen problems, like the bathroom collapsing, but it will limit issues that may arise with new work.
MELTDOWN #3: The Lights Go Out on Broadway
The Scenario: A large co-op in Flushing is separated into two sections, north and south, each with its own elevator. Recently, the north elevator was replaced, which meant only the south elevator was operational. While this was somewhat of an inconvenience—residents on the top floors had to walk across the roof to access their apartments—it was necessary to modernize the equipment.
While the repair was going on, a circuit blew. There was no power to the common elements, including the elevator that was being repaired, and no lights in the lobby or hallways.
The managing agent, Mark Levine, vice president of Excel Bradshaw Management in Carle Place, sprung into action. The first order of business: assess the problem. "Is it a fuse in the circuit box?"
The answer, resoundingly, was no. "The electricity blew underground," he says. "A 50-year-old underground cable."
Levine dispatched an electrician on an emergency call, who re-routed some wires, so lighting was restored to the hallways, lobby and other common areas.
The good news: the south elevator—the one that was still open—ffected. The bad news: because there was no basement, there was no way to access the damaged cable. This meant that the wires had to be removed—up from beneath the foundation like so many copper weeds.
"They were huge wires," says Levine. "It took an electrician with a rig to pull them out. It took 10,000 pounds of force. At first, we couldn't find a rope strong enough. We broke three heavy duty cables."
It was determined that rather than re-install cables underground, the whole building should be re-wired on the outside. One electrician submitted a bid that Levine felt was too high.
"We did due diligence," he says. "It was an emergency, so we couldn't scope it out like we usually would, but we had another electrician come the very next day."
The Lesson: As with the case of the collapsed bathroom, the blown wire was not foreseeable.
"It's just one of those things," Levine says. "Cables go when they go."
The lesson here: when mishaps occur, use the opportunity to modernize. The mistake made it the original design— electrical wires in inaccessible places, beneath concrete—rected so it will never happen again.
"We wired it on the outside, so it can be accessed," he says.
The job ended up costing $12k, with the bulk of the expense being the new wires. This is another lesson: it always pays to have money in reserve in case of rainy days— without electricity.
Greg Olear is a freelance author, editor, web designer, astrologer and stay-at-home dad living in Highland, New York.
Leave a Comment