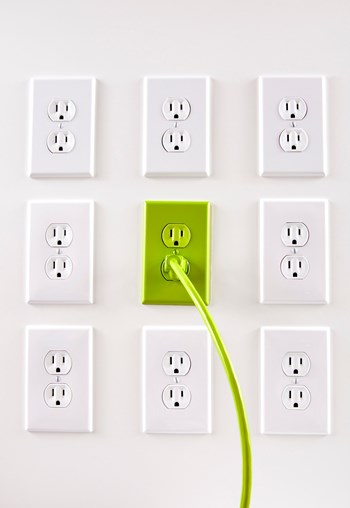
There are a number of consultants out there that are “pretending” that they can prepare the energy audit and energy efficiency reports required by Local Law 87.
Local Law 87 of New York City's Greener, Greater Buildings Plan requires all buildings over 50,000 square feet to file an Energy Efficiency Report (EER) with the New York City Department of Buildings. The EER consists of an ASHRAE Level II energy audit and retro-commissioning study of base building systems.
Energy Efficiency Reports are due once every ten years. The first reports must be filed by 2013, and are due in a staggered schedule based on the last digit of the building's tax block number. Both the energy audit and retro-commissioning study must be completed within four years before the EER is filed.
I had the recent unfortunate opportunity to review an energy efficiency report that was poorly prepared and of almost no use to the client.
Be Prepared
Needless to say, you cannot wait until December 1, 2013 to start preparing a report due on December 31, 2013. It may take your consultant several months to prepare the energy audit report, and in some cases, it might take 6 to 18 months to fully implement the recommendations.
The energy audit report is supposed to tell you what operations and maintenance work, and capital improvements, are needed in the building to reduce energy use. Once you get the energy audit report, you are required by Local Law 87 to complete the retro-commissioning work.
Some of the work may be minor, for example, a boiler cleaning. Other work may be major, for example, replacement of an oversized boiler—in which case, it might take an engineer several months to select a smaller boiler. It can take from 6 to 18 months from start to finish to complete a major job such as this.
What can go wrong? As Murphy’s Law tells you, almost everything. Let’s start with some basics:
The energy audit report should have a page summarizing energy usage and costs for the past one or two years for fuel oil, natural gas and electricity. It should also provide a baseline cost of each of the units of energy to be used in the report’s calculations.
For the cost of oil, the question is whether to use the present cost of the last delivery or the average cost over the past year. I recommend to use the most recent cost, as it is difficult to predict the future cost of oil. If the last delivery was several months ago, I prefer to call up the supplier and use the present cost.
For natural gas, your consultant should not use an average cost per therm from the last bill, but rather should look at the incremental cost of the last therm of gas, plus any applicable taxes and surcharges.
For electricity, if you are billed for energy and demand charges, your consultant should break down these charges. There may be distortions in the energy cost savings calculations for certain energy conservation measures. For example, an energy conservation measure involving lighting that is on 24 hours a day, 7 days a week may distort the cost savings if an average cost per kWh is used in the calculations.
Each energy conservation measure should be on a separate page. It should begin by describing the present condition. It should describe the recommended energy conservation measure. Energy saving calculations must be based on sound science. It should provide a verifiable calculation showing how much energy will be saved by the measure. A cost estimate needs to be provided for the energy conservation measure, and a basis for the cost. A simple payback period needs to be provided.
Energy conservation measures should not engage in double accounting of energy savings. For example, tuning up a boiler may raise its steady state efficiency from 75 to 80 percent. A calculation for the energy savings to insulate a steam line should be based on the 80 percent efficiency rate, not the 75 percent efficiency.
Is Your Heating System Oversized?
The report that I saw had a calculation for replacing a 5-ton lobby air conditioning system with a more efficient system. There was no load calculation to determine if the 5-ton A/C system was oversized. And in this case, a smaller system may have been more efficient and cheaper to install.
Also, the basis for the energy savings calculation was based on a guess of the number of hours the system was running; it was not based on any actual measurements. It was assumed that the system was running continuously; A/C systems do cycle. The fan may run continuously, but the compressor may cycle. Also, the cost of the installation was too low, making the potential payback period appear shorter than reality. Additionally, no mention was made of a need to clean the ductwork.
Another factor is that the heating description was incomplete. The report mentioned the make and model of the steam boiler, but did not tell whether it was a one-pipe or two-pipe steam system. No mention was made of whether the boiler had adequate insulation. There was also no inventory of the uninsulated steam lines; I have yet to see a building in New York City which has adequate steam pipe insulation. If your boiler room is over 65 degrees, your boiler or your steam lines, or both, do not have adequate insulation. No mention was made if the outside air to supply the boiler room had a solenoid-activated damper in series with the boiler controls to keep cold air out of the boiler room when the boiler is off.
It was also not clear if the boiler was oversized for the building. No inventory was made of the attached steam radiators to determine the total BTUs necessary to get steam to all of the radiators at the same time. One must compare the attached radiation load against the firing rate of the boiler. It was not clear if the radiators were oversized; once you put double-glazed windows in a building, your radiators become immediately oversized which leads to overheating situations. In this case, you need to put smaller radiators in the building. Thermostatic radiator valves can be great, but sometimes putting in smaller radiators is actually much cheaper.
Any calculation that is based on a “percentage” must be treated as suspect. Any consultant that relies on manufacturer’s literature rather than sound engineering principles can be prone to inaccuracies in their reports. My advice is to question everything. Use best practices and practical engineering rather than guesswork to avoid any problems down the line.
Daniel Karpen is a Long Island-based professional engineer and consultant.
2 Comments
Leave a Comment