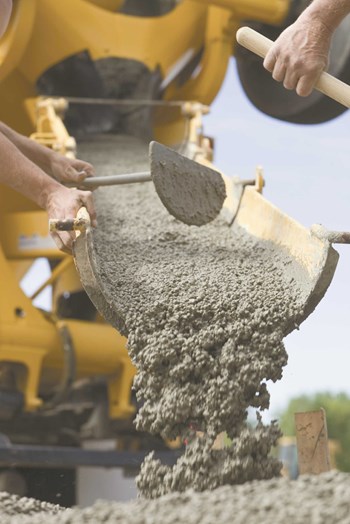
In New York City, urban high-rises with sidewalk frontage and outer-borough HOAs with walking paths, parking lots, and service roads are reliant on their paved surfaces and therefore need to regularly inspect and maintain their concrete.
Concrete Facts
While the terms cement and concrete are often thrown around as being interchangeable, cement is actually an ingredient of concrete.
“Concrete is a mixture of white sands, large aggregates and cements. All three of them comprised together make concrete,” says paving specialist Mario Sciacca of Etna Contracting in Red Hook, Brooklyn. “So when people refer to cement work, that’s wrong; it’s concrete work.”
Good concrete can be obtained by using a wide variety of mix proportions if proper mix design procedures are used. A good general rule to use is the rule of 6’s: A minimum cement content of 6 bags per cubic yard of concrete, a maximum water content of 6 gallons per bag of cement, a curing period (keeping concrete moist) a minimum of 6 days, and an air content of 6 percent (if concrete will be subject to freezing and thawing).“There is a wide variety of concrete mixes used throughout the New York City area,” says Sciacca. “But the New York City standard code is for 3,200 psi, which stands for pounds per square inch. But the industry normally uses 3,500 to 4,000 psi. The higher the psi, the better and the stronger the concrete would be but it also withstands the salts and the calcium chlorides much better than a lower psi concrete.”
To increase the strength and durability of heavily used surfaces additional thickness and reinforcement can be used. “The typical mix for house foundations and condo building foundations in Manhattan is 3,500 psi,” says Matthew Koerner, president of Manhattan Concrete Design in New York City.
Cracking Up
Concrete, like all other materials, will change slightly in volume as it dries out. In typical concrete, this change amounts to about 1/16 of an inch in 10 feet (or .4 cm in 3 meters).
“Concrete expands and shrinks, so contractors put joints in concrete pavements and floors,” says Sciacca. “It allows it to flex without causing cracking in the concrete. There are two types of joints; an expansion joint which is the wider one that you normally see with the corking and then there’s control joints. Control joints will create a pattern of some sort. People think its aesthetic but it’s not. Control joints look for the weakest point within the concrete, so when it cracks, it cracks into that control joint.”
The two biggest maintenance issues that are associated with paved surfaces in high-density urban environments are surface spalling and cracking.
“The number one cause of spalling in New York City is deicing chemicals, ice melters, and salt,” says Koerner. “If you are using that on concrete it will cause spalling. When the deicers start to melt, the salt, water and acid combination is really bad for concrete. That chemical reaction causes spalling. Extreme weather, temperature change, expansion and contraction will also cause concrete to crack and spall.”
When it comes to the actual installation, there are a number of things a building’s staff can look out for to make sure that shortcuts aren’t being done that can compromise the longevity or strength of a paved/concrete surface.
These include an inadequate sub-base, a lack of reinforcement, either no wire mesh or fibers in the mix, poor finishing techniques, inadequate joint spacing, general sloppiness from start to finish and improper curing.
“Curing is the procedure for maintaining an acceptable moisture content,” Sciacca says. “The curing process depends on the time of year. In the winter time we put insulated blankets over the concrete to keep the heat inside because you don’t want that heat to escape too quick. You want to keep it there for it to cure properly. In the summertime what happens is the sun is hydrating it too quick so what you do is you put cure seal on it and that stops the moisture from escaping.”
Concrete surfaces can also flake or spall if the water/cement ratio is not as low as possible to improve durability of the surface. Too much water in the mix will produce a weaker, less durable concrete that will contribute to early flaking and spalling of the surface.
“The finishing operations should not begin until the water sheen on the surface is gone,” says Koerner. “The sealer and epoxy is applied about 27 days after the placement of the concrete.”
A Sound Surface
In addition to inspections, there’s plenty of action that an association’s staff can do to keep its concrete in good repair and maximize its life span. Sciacca offers the following checklist to keep it top-notch at all times.
• Keep the concrete generally clean and free of debris
• Do light pressure washing to remove dirt and stains
• Repair deteriorating expansion joints with polyurethane caulk
• Caulk large cracks with self-leveling epoxy caulk
• Repair damaged concrete with a rapid set concrete mix
“You should seal concrete surfaces with commercial grade sealer. A curing compound acts to prevent moisture from leaving the concrete during initial stages of strength development,” he says. “There are numerous sealers on the market. We get garden sprays and put the sealer in the garden sprayer and spray the entire surface with it.”
Many sealer applications are effective for a two-year period but the use of deicing chemicals during the first year of service is not recommended, especially if concrete is installed late in the year. Sand is an acceptable alternative anytime.
It’s recommended that you never use deicers containing ammonium sulfate or ammonium nitrate, as they will chemically attack and rapidly disintegrate concrete.
Advancements Abound
New formulations and technologies have come along over the years that have improved the performance, appearance and life span of concrete and pavement.
The mission of the National Concrete Masonry Association in Herndon, Virginia is to advance and support the concrete masonry industry through research and programs.
“Through our NCMA foundation program we have given out thousands of grants,” says Michael Maroney, a production specialist at NCMA. “Once a year we get grant requests and the engineering staff will sit down and go over them and check recommendations. We’ve given out grants for a life cycle study of concrete and research on concretes’ environmental impact and grants on ways recyclable materials, aggregates and admixtures can prolong the life of concrete. Concrete is constantly evolving.”
In 2003 the Yangtze Dam Project (a hydroelectric dam that spans the Yangtze River) in China, inadvertently started a concrete research frenzy, said Maroney.
“During the building of the Yangtze Dam, China was paying top dollar for cement being produced in the United States,” says Maroney. “What happened was that it kicked off a renaissance. People began to think ‘how can I make concrete not only better, but more efficient?’ People started experimenting with different things and looking at alternative materials like granulated furnace slag. The whole green movement began happening with concrete.”
Concrete powers a $35 billion industry in the United States and employs more than two million workers across the country. Over 55,000 miles of concrete spans our nation’s highways. Reinforced concrete, pre-stressed concrete and precast concrete are the most widely used types of concrete.
Insurance Issues
In New York City, the concrete laws are overseen by the Department of Buildings and the Department of Transportation (DOT). New York City law requires property owners to, at their own cost, install construct, reconstruct, repave and repair the sidewalk adjacent to their properties, including the intersection quadrant and pedestrian ramps for corner properties.
Problems can result when the pavement is too thin for heavy loads such as garbage trucks and other utility vehicles. By contrast, a thicker-than-necessary pavement drives up installation costs. Problems also occur when sections of pavements or sidewalks are heaved out of alignment by tree roots, or damaged by heavy maintenance vehicles. For these reasons, tree growth should be monitored, and sections of sidewalk crossing parking lot entrances should be poured thicker.
One of the common failures, which can occur on a concrete parking lot, is around drainage structures. Inadequate compaction of backfill material around these structures can result in loss of support for the pavement.
When it comes to protecting yourself legally with cement and paved surfaces, every community association should have general liability coverage.
Problems can also lead to large court settlements.
“The nuance with slip-and-fall lawsuits in a co-op is that the lawsuits will come from a tenant shareholder,” says Dean M. Roberts, an attorney with the Cooperative & Condominium Law Group of Norris McLaughlin & Marcus in Manhattan. “Unlike a landlord who may end up with a tenant slip-and-fall lawsuit, in a co-op you have a tenant shareholder who’s technically a shareholder of the corporation they are suing. And what has been an issue lately is when the shareholder is also a member of the board of directors. I’m seeing more and more co-ops making a rule that if you’re on the board of directors you can’t be a party to litigation against the co-op.”
There are numerous precautions shareholders and property owners can make to avoid lawsuits. “The recommendation is to have a set policy, a clear protocol for spills, water leakage on rainy or snowy days. On rainy days we do X-Y-Z,” says Roberts. If an area is under construction, for example, the experts advise cordoning it off with a plastic cone or yellow tape.
In the end, the key to avoiding pavement problems is to prevent them in the first place through proper installation, conscientious maintenance, and a quick response to damage.
Keith Loria is a freelance writer and a frequent contributor to The Cooperator. Staff Writer Christy Smith-Sloman contributed to this article.
Comments
Leave a Comment