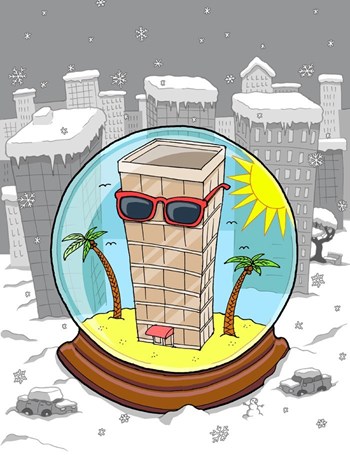
Despite the heavy rains, which kicked off this summer season, the thoughts of beaches, vacations, barbecues, family picnics and ball games still permeate the air. The last thing on most people’s minds is the icy chill of winter. However, for those in the know, the summer months are actually the best time to prepare buildings for the harshness of the coming winter season.
“Usually we recommend the spring and summer months to begin the process of checking systems for the coming winter,” says Frank Alimossy, a service technician for Brooklyn’s Aggressive Energy & Mechanical Group, an HVAC and boiler maintenance repair company. “This is not something that should be put off,” he continued. “Building owners should make it an annual event.”
In order for a building’s operating systems to run safely and efficiently, a system of checks and balances must be in place. This requires a thorough understanding of all the components that ultimately deliver the essential amenities like heat, air conditioning, water, plumbing and electricity.
Delegating the responsibility for maintaining these building systems is something that the superintendent and staff normally handles, although they should coordinate with the managing agent and the board to insure all issues are addressed in order to prevent situations like no heat in the middle of January.
“Without due diligence, problems can and will arise,” says Gregg Annunziata, director of sales for Metro Builders LLC, serving clients in New York City and New Jersey. “In some cases superintendents or building managers can run down a list of checks and balances, but in some cases additional oversight is required because they might miss something that could turn into a significant problem down the road.”
From the Bottom Up
Peter Grech, president of the New York Superintendents Technical Association (NYSTA), agrees with Annunziata in regard to a superintendent’s duty, but he stresses the need for additional supervision.
“Most supers can handle the inspection task and minor correction repairs. Though when there is problem or a potential problem, it’s best to call a repair company or two and get proposals,” says Grech. “Remember supers can only do so much. Should the [in-house] repair fail and [should] damage occur, if done by the contractor there is insurance, if done by staff, [there is] no insurance.”
Like the human body, a building’s operational systems are vital to health and comfort of its residents. Its integral elements include all the components of the heating, ventilation and air conditioning systems, commonly known as HVAC—the boilers, chillers and compressors, as well as the generators, plumbing, pumps, electric panels and gas systems. However, it is the building’s age, which often dictates the reliability of one or more of the aforementioned systems. While some buildings are celebrating their thirtieth or fiftieth anniversaries, others are youngsters.
“We work on buildings of all ages and sizes,” says Alimossy. “Among the things we look for is oil quality—meaning that there is no dirt or grit and that piping is not white and corroding, which leads to leaking.”
Alimossy explains that additional inspections are required to detect any damages done to the functional efficiency of the chimney. “If there is white steam that means there is a leak somewhere. Black smoke means there are problems with the oil.”
Many utility and energy companies offer boiler tune-ups for around $500 to $700, plus parts. This approach, notes Alimossy, is not unlike regular maintenance on a car. “Even if you’re operating system is a hair off you could lose between five and 25 percent efficiency each day,” he continues. “The investment can be recouped in one really cold winter’s day,” he adds.
This annual inspection is not just recommended for older operating systems. Regardless of age, boiler inspections should take place every year, notes Annunziata, adding that new systems are usually under warranty. “It is recommended to consult with manufacturers of equipment to determine frequency of service maintenance,” he says. Backup parts, he added, should be purchased during the summer so they are stocked and prepared come winter.
Water and Power
Since a building requires electricity to run many of its vital systems such as lighting, heating, hot water, appliances and air conditioning, it is paramount that its electric capacity levels are known. For example, certain older buildings may not have enough outlets or circuits to support the demands of modern electrical usage.
In addition to scheduled checkups, one way to avoid electrical outages is to require homeowners to obtain permission from managing agents and superintendents prior to adding appliances.
When it comes to addressing plumbing issues, there are a plethora of items to investigate—including pipes that bring water and heat to fixtures, pipes for sewage and drainage, gas supply lines and underground sprinkler systems. Inspections should also center on the water meter, water supply pressure, water supply line materials, plumbing fixtures, drain lines, gas lines and hot water and steam heat piping.
“One of the biggest concerns of many homes and buildings is leakage,” says Annunziata. “And sometimes the leak is internal, and it is discovered when it is too late and significant damage has occurred.”
Not unlike a trip to the doctor, or a scheduled oil change, operating systems should be inspected and maintained on a regular basis. In most cases, insurance companies require annual inspections, as do local municipalities. However, this may not be enough to ensure peak performance.
Inside Out and Outside In
With internal operating systems covered, superintendents and building managers have to address the brick and mortar aspects of the building. For example, the freeze/thaw cycle can loosen brick, stone, precast concrete, wood and flashings from a buildings’ exterior. Additionally, drainage lines can be compromised. Telltale signs include grass growing on roofs and drains.
While the aforementioned are usually considered cosmetic, it can underscore structural integrity issues. “Visual inspections help with prevention, and is the proactive way to go,” says Grech.
Properly-insulated buildings will save significant amounts of both energy and money. The biggest culprits are windows and doors especially in older buildings. Superintendents can inspect windows for drafts using forced air and binoculars (to visually inspect spaces and gaps). While it may be expensive, investing in new energy efficient windows is a smart investment.
The New York City Department of Buildings (DOB) offers the following tips:
• Insulate your attic. The majority of heat that escapes is from the roof. Proper insulation of at least six inches will prevent heat loss.
• Insulate windows. Windows should be properly sealed with weatherproofing materials to prevent drafts.
• Insulate doors. Even closed doors can be a major source of heat loss. Weather-stripping around the edges will help keep heat in the house.
In the final analysis, board members are responsible for ensuring that the vital operations are properly maintained. If a building or association’s bylaws are supported by a competent manager and superintendent, major problems can be avoided. In addition, a progressive board can educate shareholders and unit owners on ways they can keep respective energy costs down including buying Energy Star appliances, maximizing sunlight during winter months and keeping heat levels as low as possible when home or away.
While an annual inspection is required, the majority of buildings require supers to inspect operational systems weekly and file monthly reports. “Keep in mind a good super always checks these at least once a month,” says Grech.
W. B. King is a freelance writer and a frequent contributor to The Cooperator and other publications.
Leave a Comment